Transforming waste carbon into Sustainable Aviation Fuel, Chemicals & Plastics
Discover how OXCCU transforms waste carbon into sustainable fuels and materials.
The future of sustainable fuel and petrochemical production
At OXCCU, we have developed cutting-edge technological processes and catalysts that revolutionise the way we produce fuels, chemicals, and plastics.
We combine the biogenic carbon and hydrogen contained in waste biomass or biogas and/or CO2 from a variety of sustainable sources with additional electrolytic H2 if required, resulting in a sustainable and environmentally-friendly solution for a world without fossil fuels.
In all cases the goal is the same, lowest carbon intensity, lowest cost and highest SAF yield.
Converting green electricity to green molecules
Efficient carbon capture and utilisation process
Innovative approach to sustainable fuel production
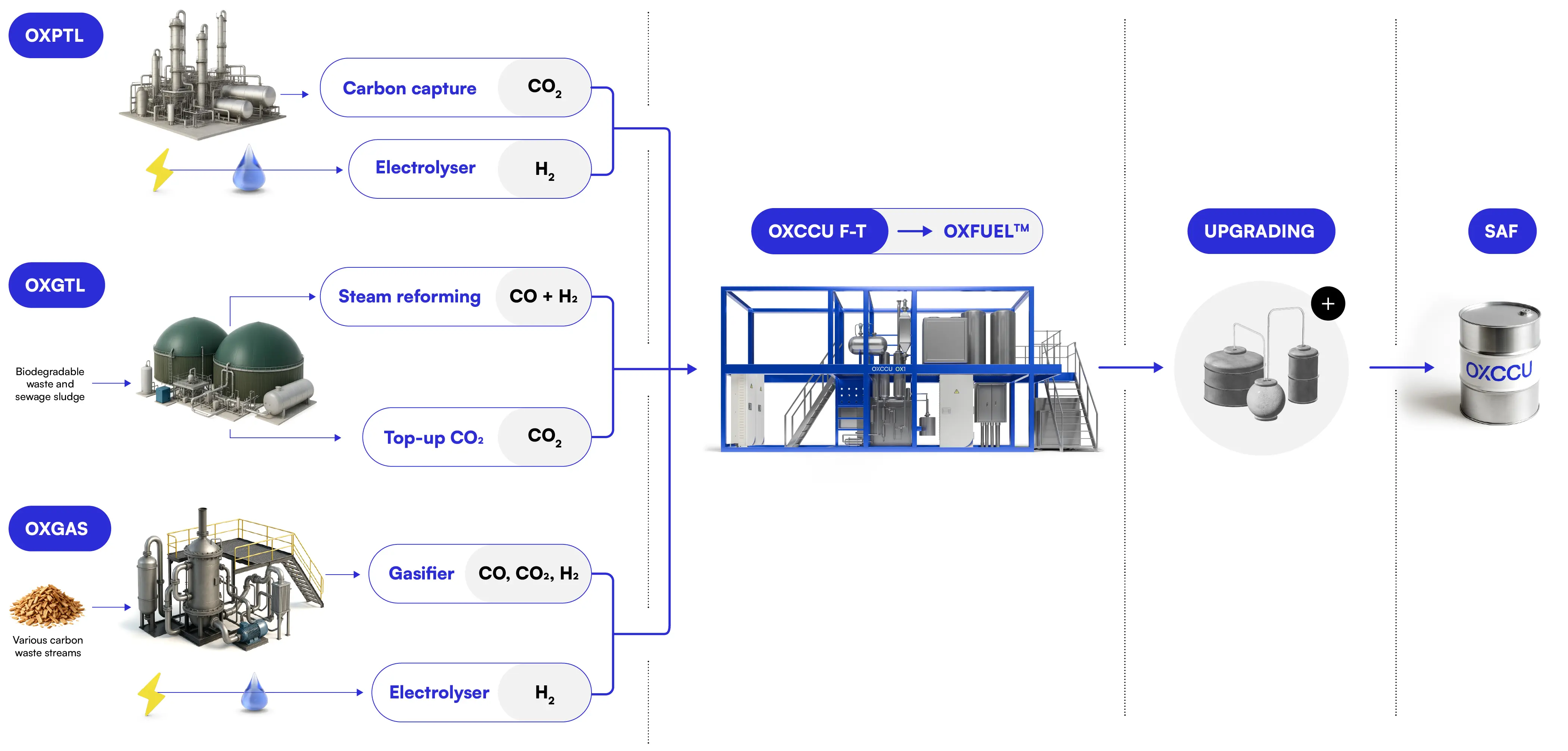
OX1 Plant
The FOAK facility, based at London Oxford Airport and designed and operated by OXCCU, has the capacity to produce 1 kg (~1.2 litres) of liquid fuel per day. Operations started in September 2024.
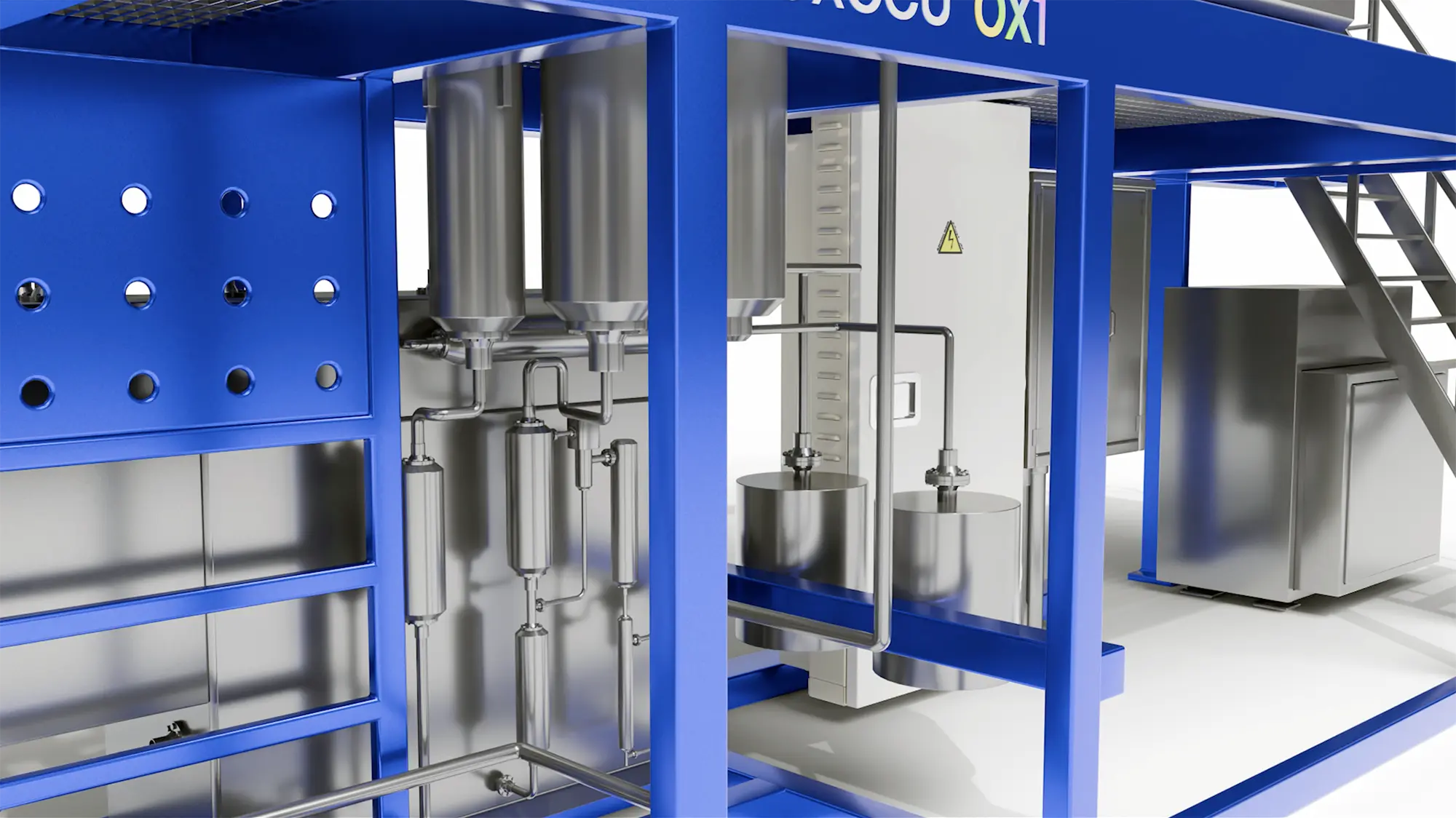
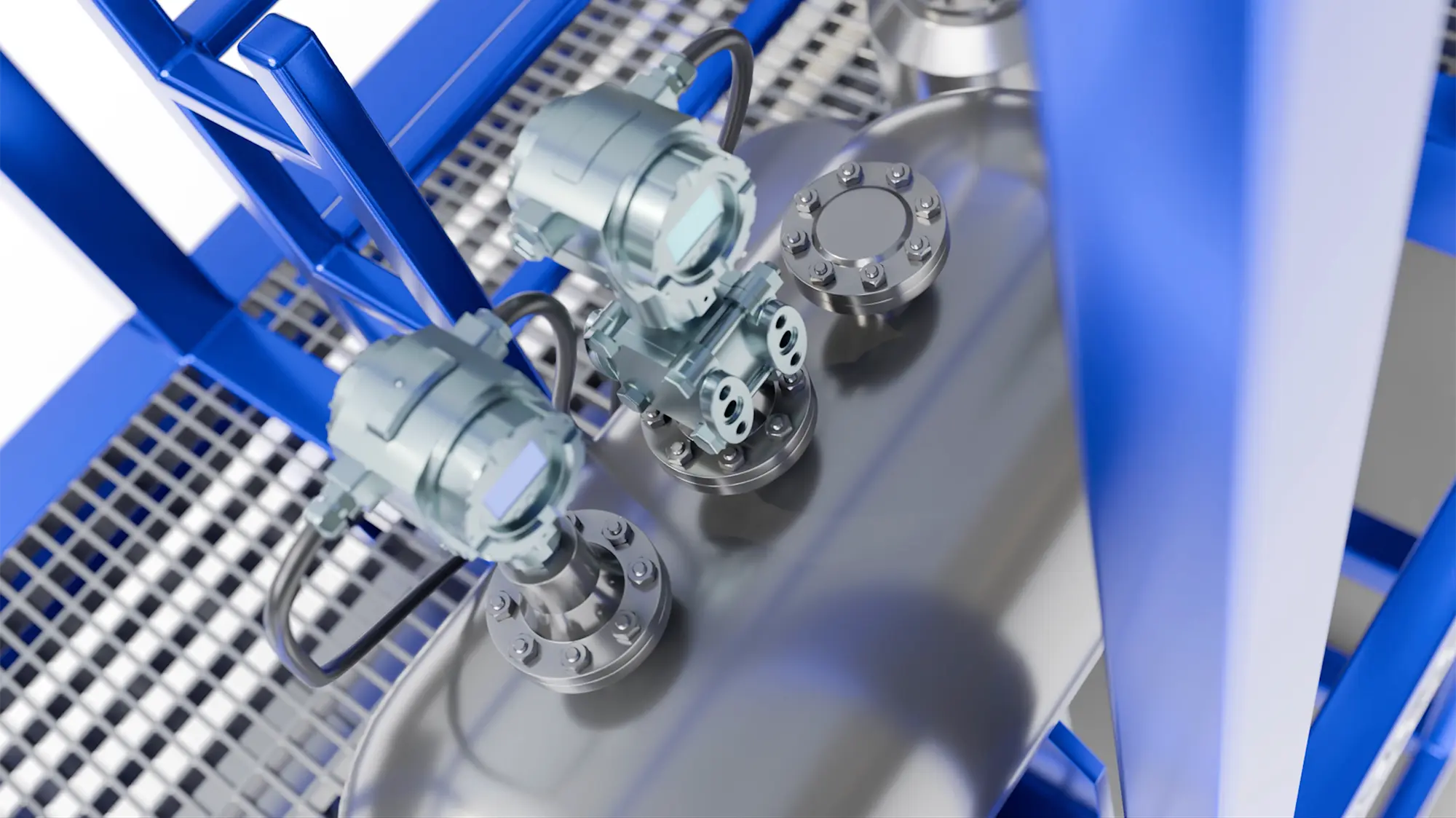
Scale-up journey
The plant is part of OXCCU’s strategic scale up journey as the first OXCCU plant out of the lab. It will provide the data key to the design, build and operations of the OX2 plant, which will operate at Oxford Airport in 2026 and demonstrate both PtL and GtL processes with reforming integration and upgrading. Commercial plants supplying the UK and elsewhere with SAF will then follow.
OX2 Plant underway
After successfully operating our OX1 pilot plant since last year, this will be our second OXCCU demonstration plant, which will be fully operational in 2026. We will produce a finished synthetic blend component using representative feedstocks on a bigger scale than we have previously. OX2 will produce 10-30 litres/day, providing even greater quantities of fuel for testing. This is another important step towards bringing cost-effective, scalable SAF to market.
The heart of the refinery of the future
Our mission is to enable future generations the continued use of hydrocarbon fuels but without their climate impact.
It is this approach which we believe will sit at the heart of the refinery of the future and allow future generations to use hydrocarbons indefinitely.
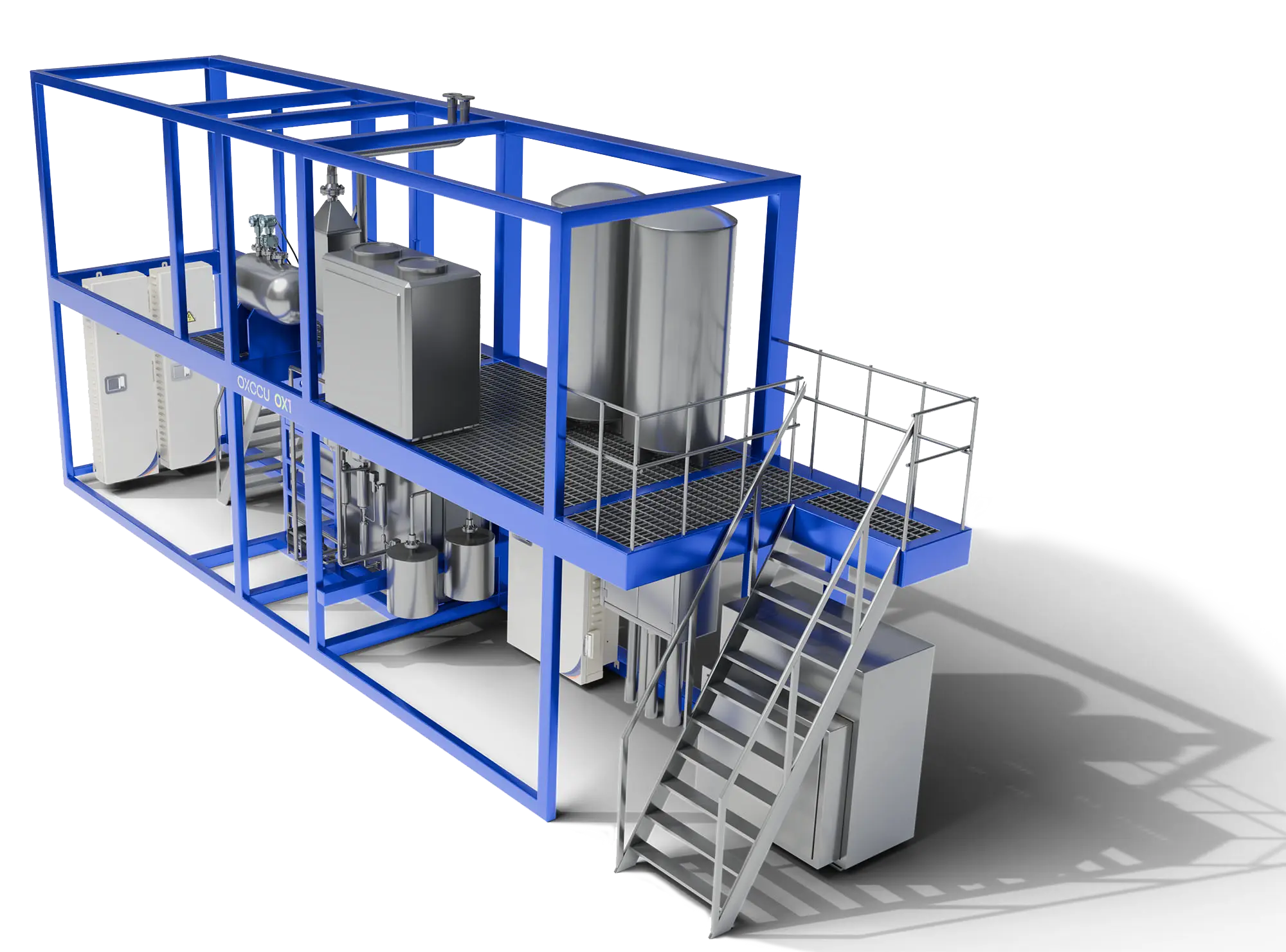
OXCCU technologies
Supported by industry leaders to develop fossil-fuel free solutions
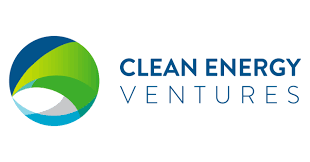
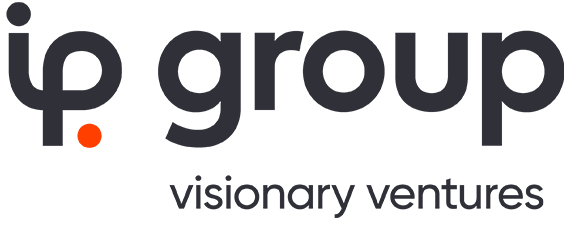
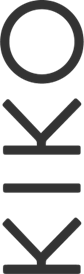
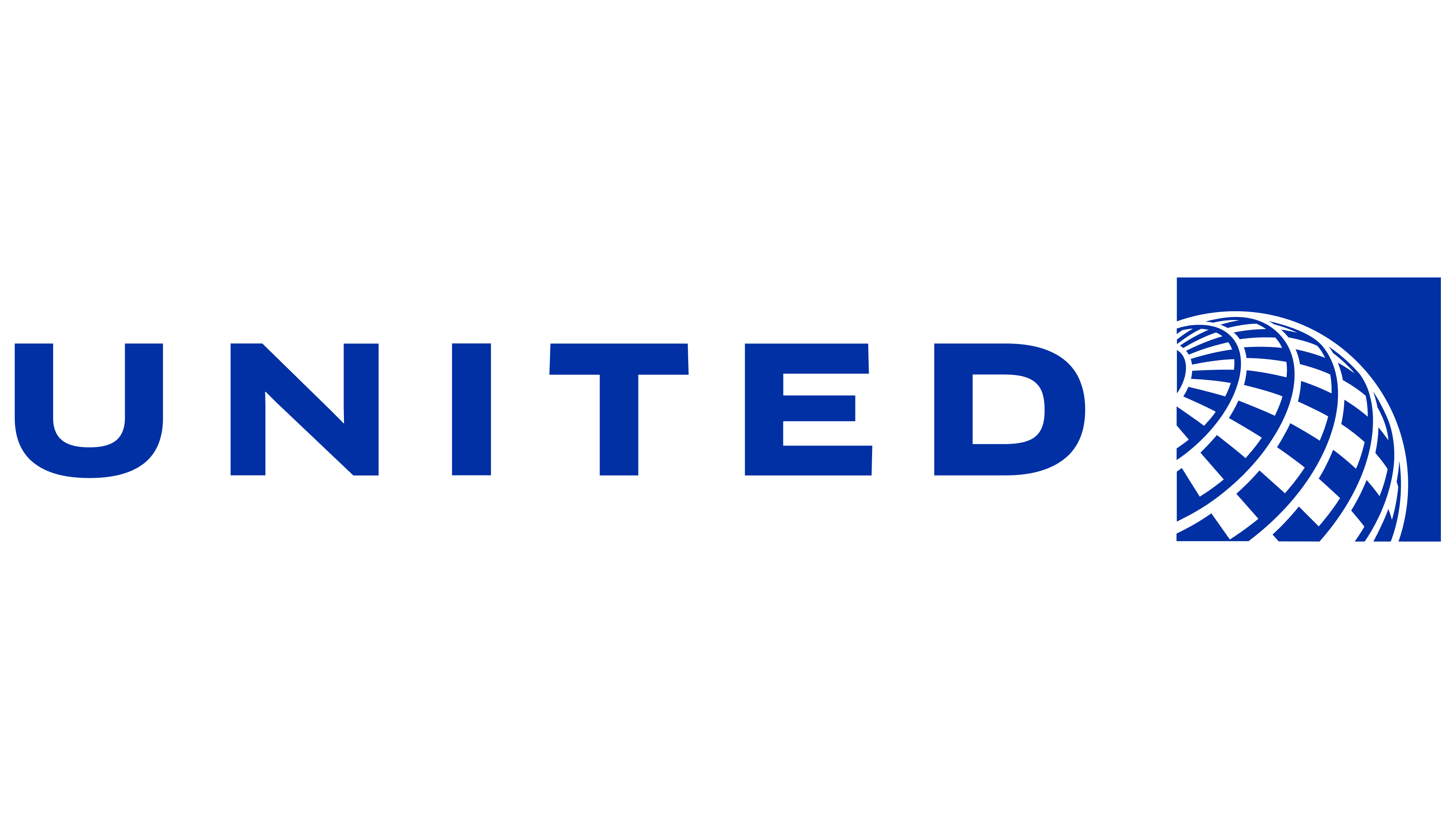
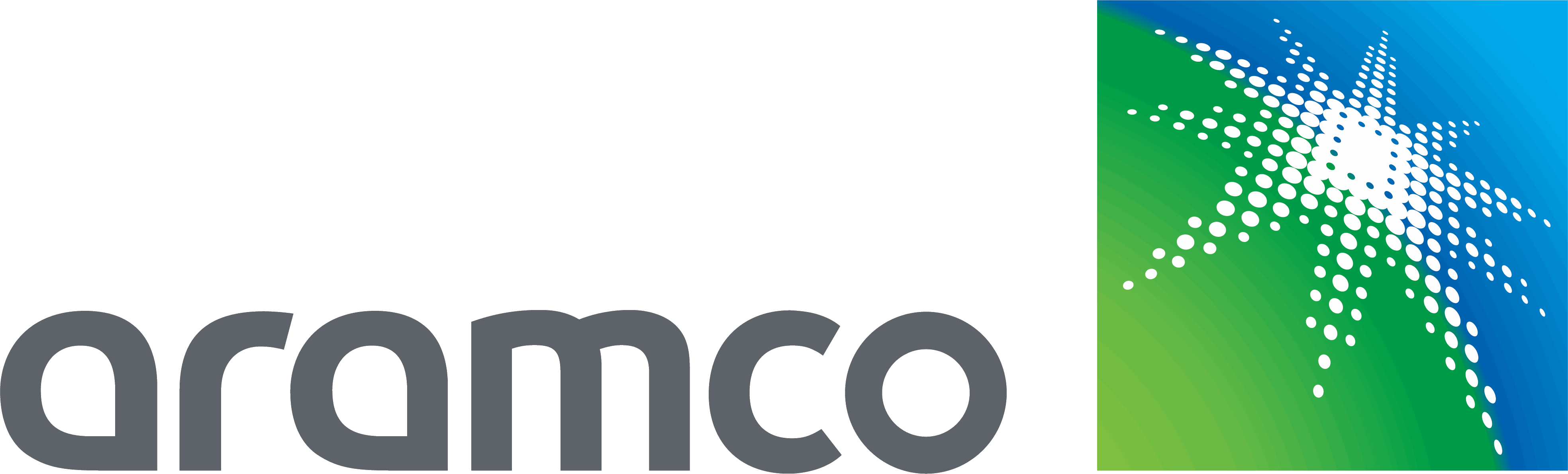
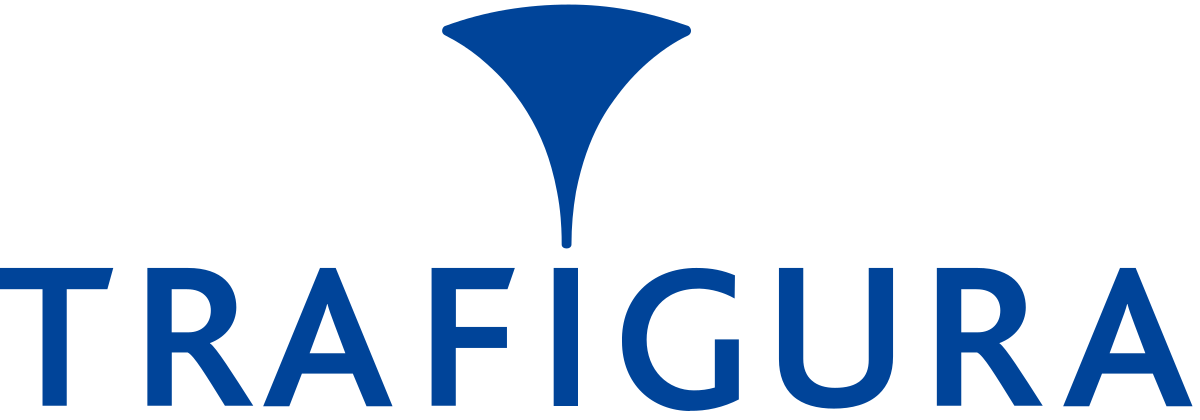
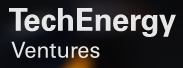
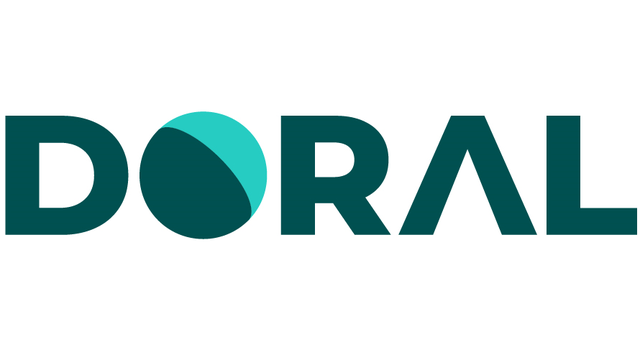
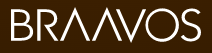
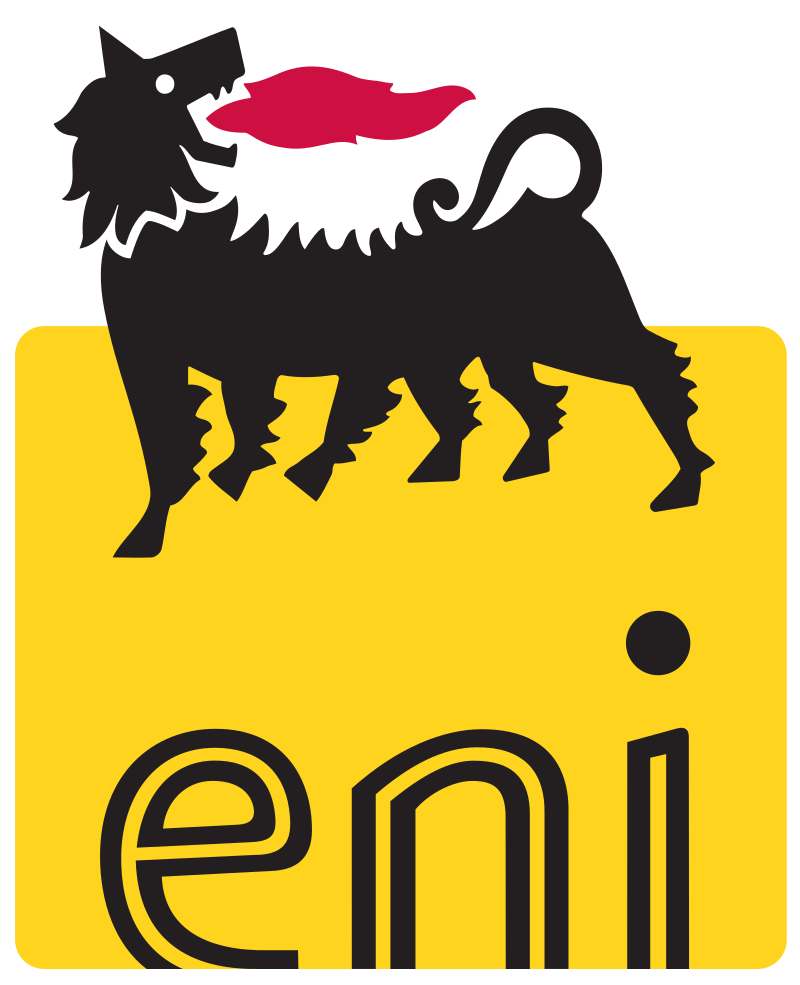
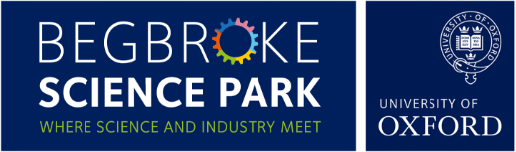
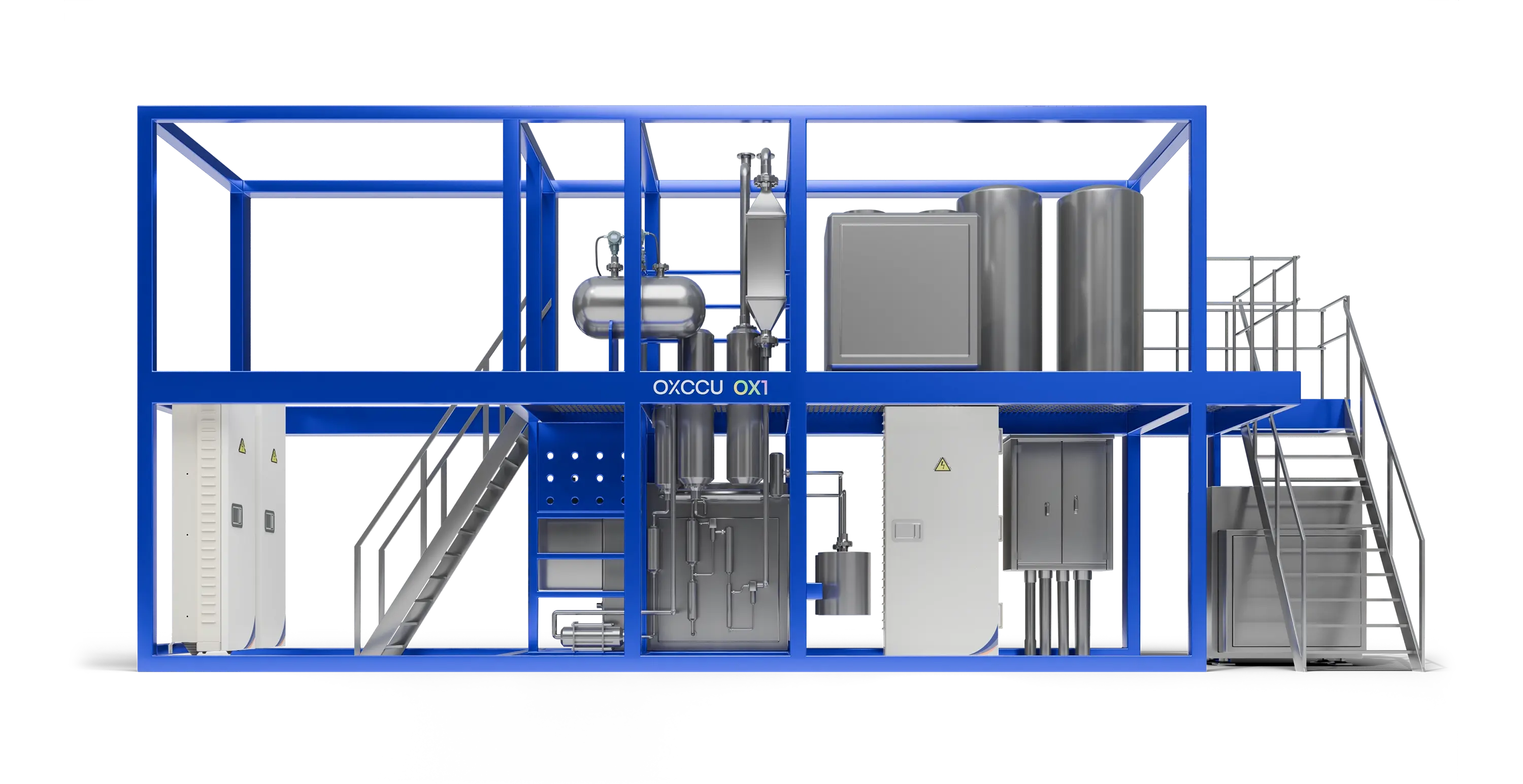
In a net zero world, we will still need hydrocarbons.
Renewables can be used directly for power and ground transport, and some sectors can use hydrogen directly, but we will still need carbon-based molecules for sustainable aviation fuel (SAF), chemicals and plastics.
- Fuels due to energy density
- Petrochemicals and plastics as carbon is the backbone of the molecules.
But with no fossil fuels, where will we get them from?
Bio-derived fuels and chemicals based on feed crops such as ethanol or vegetable oil have well-known issues at scale due to limited feedstocks, land use, and competition with food. Some industrial flue gases containing CO and CO2 can also be converted with additional green H2 if required.
The solution is utilising waste carbon.
Waste-based fuels and chemicals based on lignocellulosic waste are a key part of the mix. Waste higher in sugars, starches and cellulose can be digested into biogas and then reformed to syngas with extra CO2 added and converted.
Power-to-Liquid (PtL) or e-fuels involves the conversion of carbon dioxide produced by another process into liquid fuel using green hydrogen derived from green electricity and water. It is emerging as critical for the future of SAF, and regulation is already underway to support this transition. For example the EU requires 50% of the 2050 blending requirement under ReFuelEU to be via PtL.
To meet the huge demand we will need them all.
The challenge is cost and carbon intensity.
Simplifying and scaling processes
OXCCU is focused on reducing the cost of waste based SAF by simplifying conversion processes. Our novel catalyst and process can directly convert the CO2 as well as CO into SAF giving it a distinct advantage. We have proved that it’s possible to make jet fuel-range hydrocarbons in a single step from CO2 and H2.
Our novel catalyst
FAQs
Learn more about our technology, its applications, and its impact on the industry and environment.
A significant amount of green electricity is used to produce the green hydrogen from water via electrolysis, but our process (CO₂ + H₂) to SAF is exothermic i.e. it releases energy and we operate under mild conditions.
Hydrogen planes are very far away from being a realistic option. The advantage of SAF from power to Liquid (PtL) is there is no need for a new plane. The synthetically produced liquid hydrocarbons utilize the pre-existing fossil fuel infrastructure for transportation and distribution, encompassing pipelines and refuelling stations. The PtL SAF can be seamlessly combined with traditional kerosene, to ensure it complies with all existing jet A fuel standards. All geographical regions are expected to have SAF mandates eventually with e-fuels (PtL) sub mandates within them, with major aviation fuel purchaser regions (like the EU) having mandates already in place. Key to commercial plant locations will be access to inexpensive green electricity and therefore inexpensive green hydrogen as well as the availability of CO₂.
The key differentiator is an F-T catalyst that is able to convert CO₂ directly into long chain hydrocarbons, significantly reducing both CAPEX and OPEX when compared to conventional two-step processes. Our patented multifunctional iron catalyst converts CO₂ and/or CO and H₂ directly into jet fuel range hydrocarbons using different active sites on the same catalyst surface, in the case of CO₂ avoiding the step to first produce CO. It is underpinned by scientific breakthroughs published in top-tier scientific journals. This is distinctive amongst all other F-T catalyst who if they want to convert CO₂ first need to convert CO₂ to CO via RWGS. To our knowledge we are the only SAF company with an F-T catalyst which can directly convert CO₂ to the long chain and that does not produce significant amounts of alcohols as a byproduct. Other sustainable fuel companies typically rely on sources such as vegetable oil, used cooking oil or ethanol but they rely on crops and are limited due to land use.